World-Class Support for your Fiber Laser Cutting System
We provide a single source for every facet of service. Our products are designed from the ground up for fast service to get them, and you, back into production fast.
Service Plans
OUR SERVICE PLANS ALLOW YOU TO BENEFIT FROM TAYLOR-MADE ADVANTAGES AND EFFICIENCY.
Our improved plans provide customized packages for every level of service. Reach out to us to receive a personalized offer based on your needs.
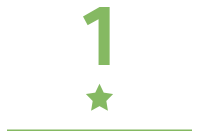
Basic Support
- 100% Telephone or remote support
- Machine parameters examination and support
- Identification of any faults
- Backup and restore to factory data of the local PC
- 15% discount on parts and labor (protection screen CLE0006 and nozzles excluded)
- SERVICE RESPONSE for machine down:
- Phone/e-mail support within 1 hour
- Internet Team Viewer support within 3 hours
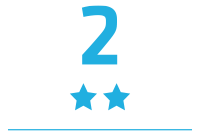
Basic Plus Support
- 100% Telephone or remote support
- Machine parameters examination and support
- Identification of any faults
- Backup and restore to factory data of the local PC
- 20% discount on parts and labor (protection screen CLE0006 and nozzles are excluded)
- SERVICE RESPONSE for machine down:
- Phone/e-mail support within 1 hour
- Internet Team Viewer support within 3 hours
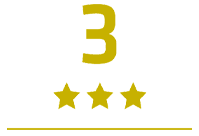
Programmed Maintenance Gold
Over the BASIC PLUS points, it includes:
- 1 YEARLY preventative maintenance intervention which includes the labor and travel costs for the following actions:
- Inspecting the system and the casing
- Control of linear guides and blocks replacement
- Centralized lubrication oil level check and topping up
- Verification of the correct functioning of the safety devices
- Filter cleaning of cooling circuits
- Chillers water level check and possible replacement or topping up
- Replacement of gases filters (Nitrogen – Oxygen – Compressed Air)
- Control of the movement of the cutting tables, control of the transmission parts and chain pawls replacement
- Check the absence of leaks in the hydraulic circuit of the pallet exchange
- Check the calibration of the GAS circuit
- Check the calibration of the LASER analog
- Checking the correct functioning and calibration of the capacitive sensor
- Checking the safety pressure switches for assist gases
- Checking the operation of the service air pressure switch
- Checking the operation of the maximum pressure relief valves of the assist gases
- Torch cleaning and consumables replacement
- Inspection and cleaning of the cutting head. Replacement of all optics and photocell window
- Control of the movement of the V axis and possible replacement of the nut
- Replacement of the vacuum head filter (Only for Light models. For EVO III and V it doesn’t apply)
- Cleaning, greasing and tensioning of the scrap conveyor
- Control of the leveling of Cartesian axes and alignment with the cutting table
- Control of the absence of mechanical slack due to the Rack and Pinion coupling of the X, Y and Z axes
- Replacement of felt lubrication pinions for the X and Y axes
- Updating the system backup maintained on the Cy-laser Server
- Sending the generator Log Files to the manufacturer for a source efficiency check
- If provided by Cy-laser:
- Spark trap cleaning and dust collector filters cartridges efficiency check
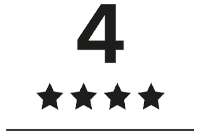
Programmed Maintenance Diamond
This option doubles the GOLD PLAN within the year of the agreement.
Assistance
United States Service Network
+1 (586) 983 9282
Canada Service Network
+1 (586) 983 9282
"*" indicates required fields